Service von Impact Innovations

Unsere Philosophie ist es, auf kundenspezifische Anforderungen einzugehen und diese durch intelligente und systematische Vorgehensweisen zu verwirklichen. Wir sind bestrebt, ein zuverlässiger Lösungs- und Geschäftspartner zu sein und den Wert von innovativen Industrielösungen durch den Einsatz von Kaltgasspritzen zu steigern. Unsere hochqualifizierten Service-Mitarbeiter unterstützen Sie gerne.
Wartung
Kalibrierung
Schulungen
Support
Impact Serviceangebot
Wir sind ein zuverlässiger Lösungs- und Geschäftspartner. Wir haben uns zum Ziel gesetzt, den Wert von innovativen Industrielösungen durch den Einsatz von Kaltgasspritzen zu steigern. Hier werden die wichtigsten Fragen beantwortet:
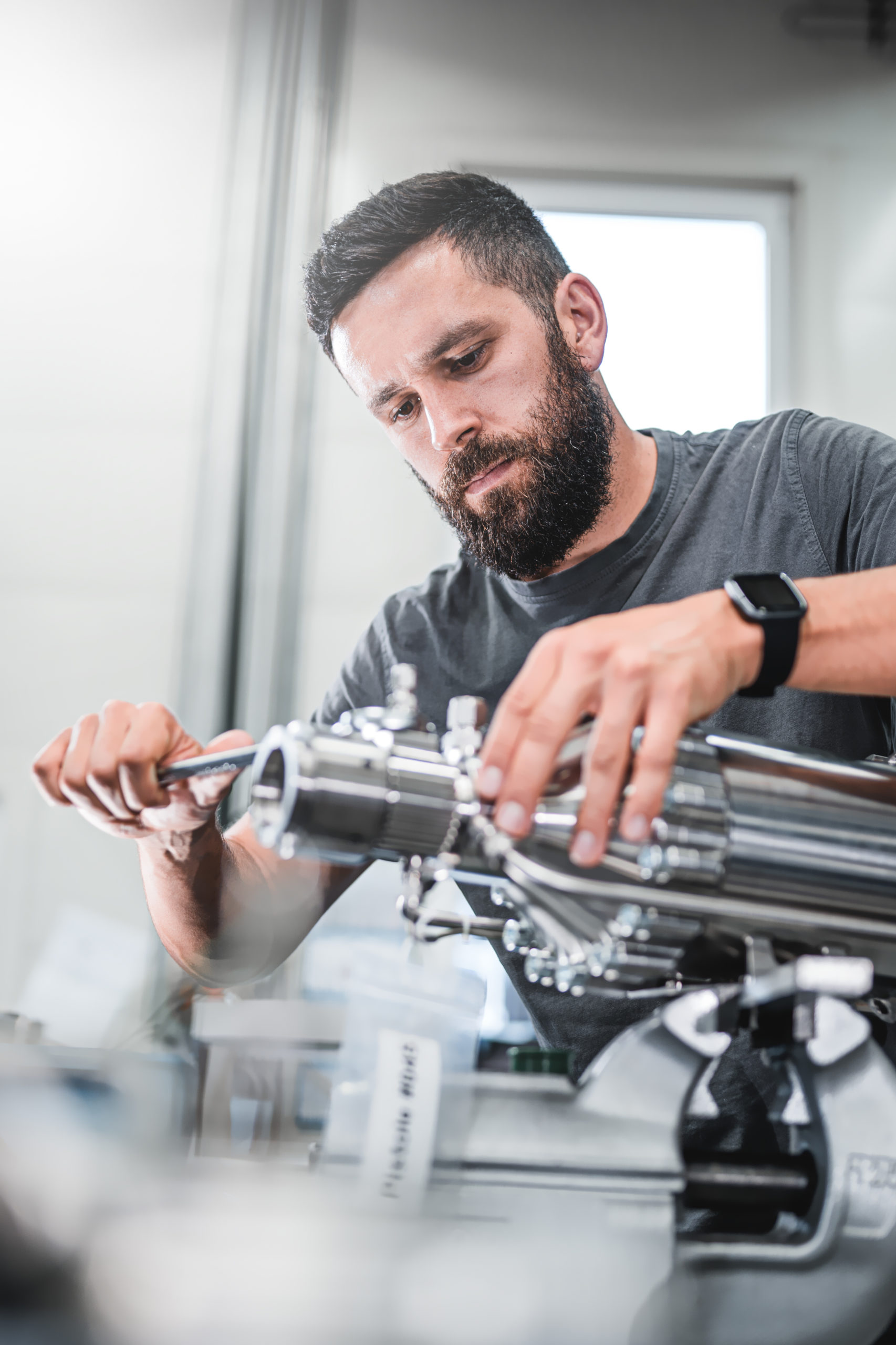
Servicevertrag
Ein Impact Innovations Servicevertrag schafft Ihnen Sicherheit!
Sie erhalten bevorzugten Zugang zu unseren erfahrenen Spezialisten im Bereich Instandhaltung, Montage und thermisches Spritzen - und profitieren zusätzlich von speziellen Sonderkonditionen. Sprechen Sie unsere Experten an. Wir erarbeiten gerne einen individuellen Servicevertrag mit Ihnen, um den Anforderungen Ihres Unternehmens bestmöglich gerecht zu werden.
- Priorisierung bei Anfragen, Wartung, Service und Support
- Präventive Wartung zum Wunschtermin
- Kalibrierung zum Festpreis
- Support Levels
- Ferndiagnosen
- Sonderkonditionen
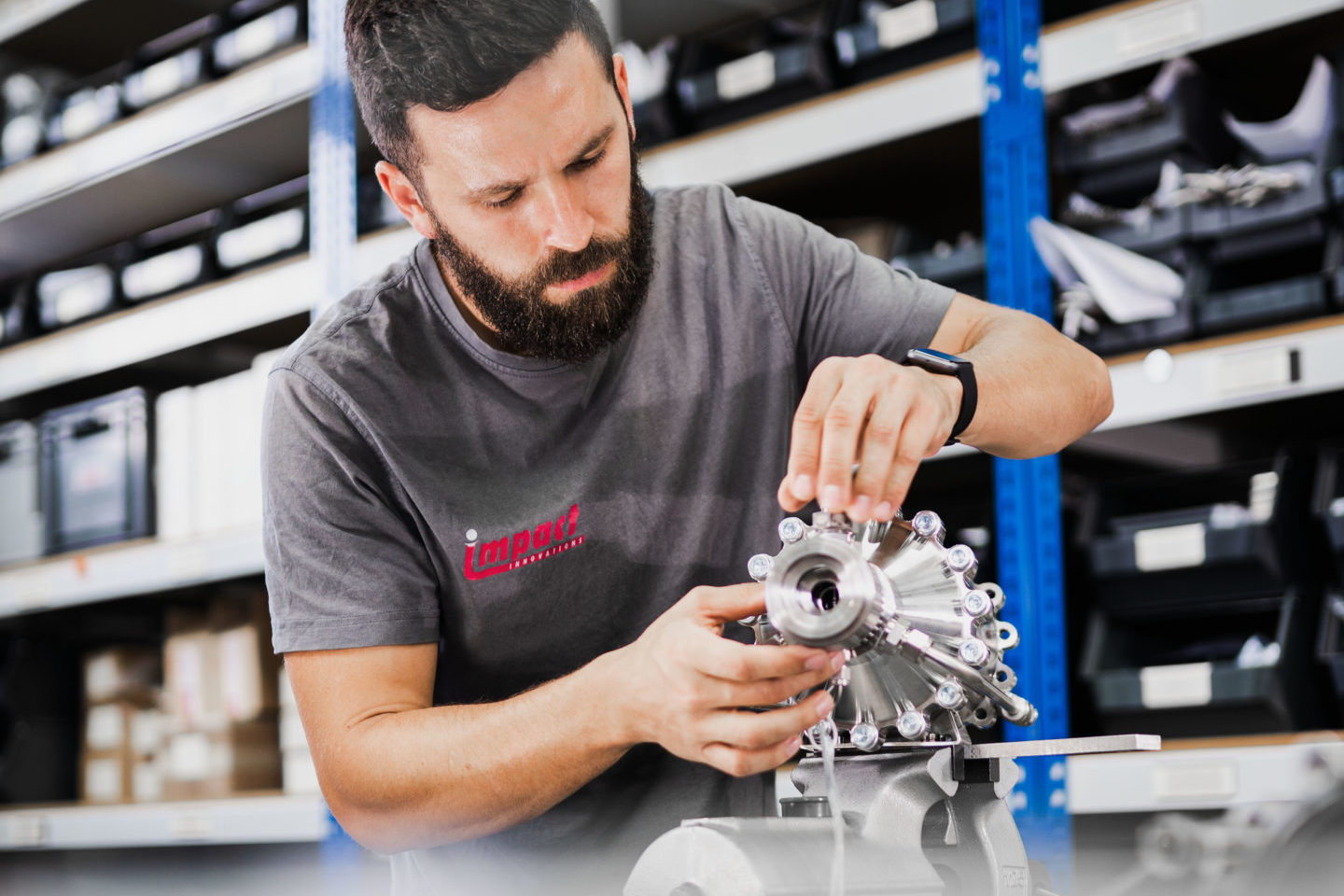
Sie haben Fragen?
Wir sind Ihr zuverlässiger Partner. Unsere hochqualifizierten Service-Mitarbeiter unterstützen Sie gerne.
Nehmen Sie noch heute Kontakt mit uns auf!