Lower emissions, less wear and corrusion: cold spray coating of brake discs for the Euro 7 standard

Uncoated brake discs are subject to high levels of wear, particularly in conventional combustion engines, and therefore emit a lot of harmful particulate matter. The new Euro 7 standard puts a stop to this pollution.
Hybrid and electric vehicles brake mainly by recuperation and only rarely mechanically. This means that the brake discs of these modern vehicles are particularly exposed to the risk of severe corrosion.
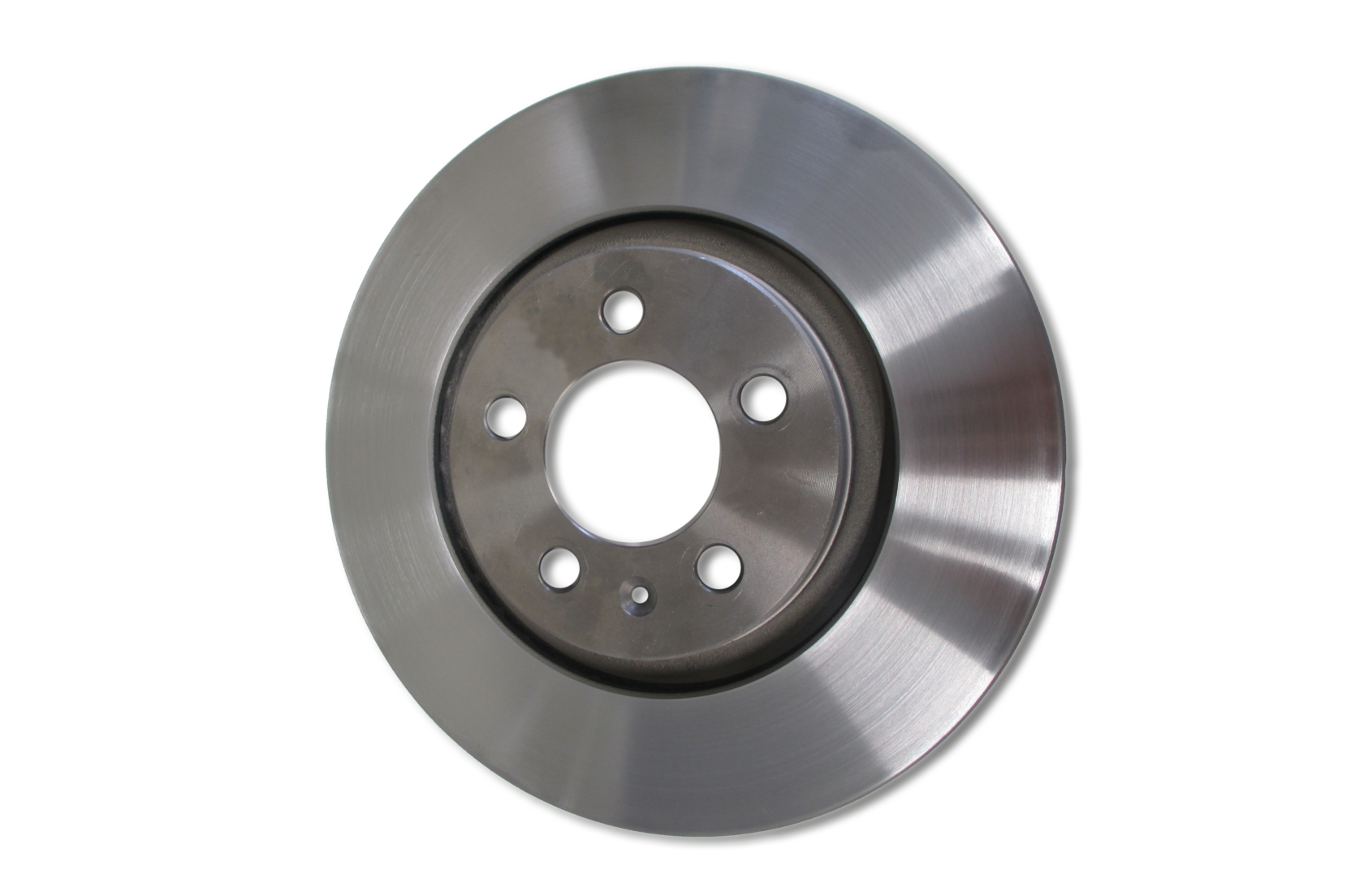
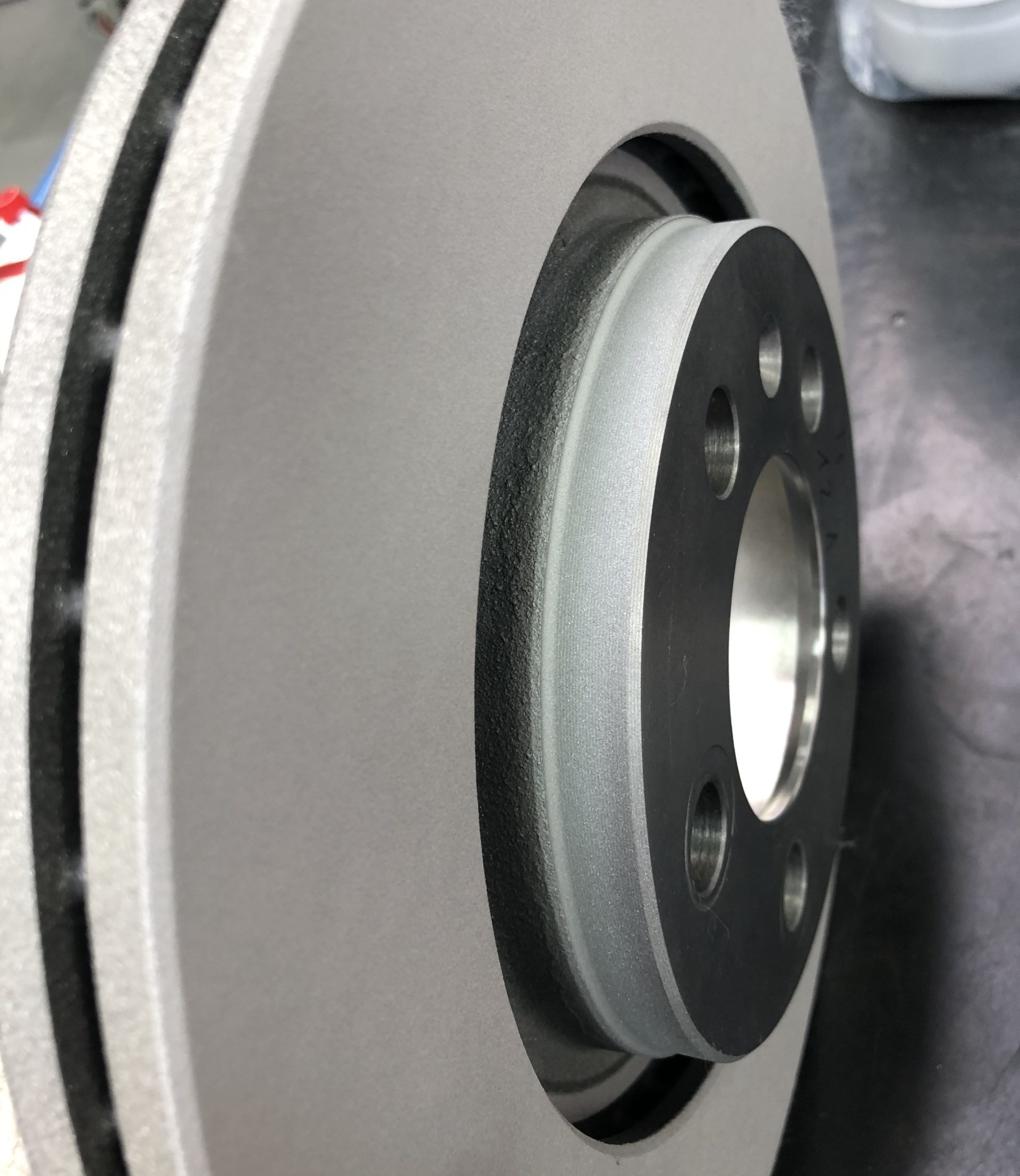
Impact Innovations offers a simple, cost-effective and extremely powerful solution to all these challenges with high-pressure cold spraying.
Conventional thermal coating processes are still very material- and cost-intensive and the required properties in terms of coating adhesion, corrosion resistance and crack behavior cannot yet be met.
In addition, cold spraying offers considerable advantages over laser deposition welding when coating brake discs to comply with the Euro 7 standard and to meet the individual requirements of vehicle manufacturers.
We have developed Impact Hybrid Brake Disc Coating® for particularly high demands on crack resistance and the lowest possible delamination of the coating, which you can find out more about here.
Tests and results
-
Very low thermal load on the brake disk and therefore no thermal distortion
-
Low porosity in the coating and low coating tolerances with low surface roughness
-
Low grinding allowance for the lowest grinding costs and cycle times
-
Simple and very robust process with identical process parameters for all designs and sizes
-
Hardly any cracking even under the toughest conditions thanks to counteracting compressive stresses in the coating
-
Full corrosion resistance after over 720 hours in the salt spray test
-
PM10 emission savings of over 95%
-
No patent protection and possible license fees from other car manufacturers
-
Minimal coating thicknesses and therefore minimal process costs for coating and subsequent sanding
- Scalable for the highest demands on crack resistance and low delamination with Impact Hybrid BDC®
Watch the coating process in this video:
