Cold Spray Additive Manufacturing (CSAM) process chain for Ti-6Al-4V with N2 as process gas

In the realm of Cold Spray Additive Manufacturing (CSAM), Ti-6Al-4V has presented a significant challenge due to its demanding nature when processed with cold gas technology. The requisite high particle velocity and resultant kinetic energy for Ti-6Al-4V processing using the cold gas technology have historically led to a layer structure porosity of 3% or higher.
However, a recently developed CSAM process, leveraging a distinctive amalgamation of cold spray hardware, process parameters, and post-treatment procedures, has achieved porosity levels below 0.5%. Furthermore, the final mechanical properties have exceeded the standards outlined by ASTM F3001, ISO 5832-3, and AMS 4930.
Unlike certain other additive manufacturing methods, Cold Spray does not entail the melting of powder particles. Instead, bonding arises through plastic deformation.
Notably, Cold Spray operates at lower temperatures, setting it apart from common technologies like laser, electron beam, or wire-arc based processes. This characteristic enables the deposition of components without the need for a protective atmosphere, and virtually without dimensional constraints, while also avoiding the emergence of thermal residual stresses. Remarkably, the efficiency of Ti-6-4 material conversion from powder to deposited form surpasses 98%.
Impact Innovations GmbH opted to showcase their novel CSAM process by fabricating a freestanding turbojet aircraft engine fan shaft using Ti-6Al-4V material. The fan shaft measures 380 mm in length and boasts a maximum diameter of 223 mm. This construction was achieved within approximately 2 hours, boasting a deposition rate of 2.7 kg/h. The final machined fan shaft carries a net weight of 3.2 kg.
The fan shaft was deposited onto a pre-machined Al alloy mandrel. Subsequent to the Ti-6Al-4V deposition, the mandrel was removed through chemical dissolution. The fan shaft demonstrator then underwent tailored post-treatment procedures to attain the desired mechanical properties. Following this, the piece was turned to achieve the final outer design and supplementary features were incorporated through conventional subtractive manufacturing techniques.
The Ti-6Al-4V alloy is notably utilized in marine and defense contexts, as well as for the production of aerospace structural components, gas turbine parts, and biomedical implants and prosthetics.
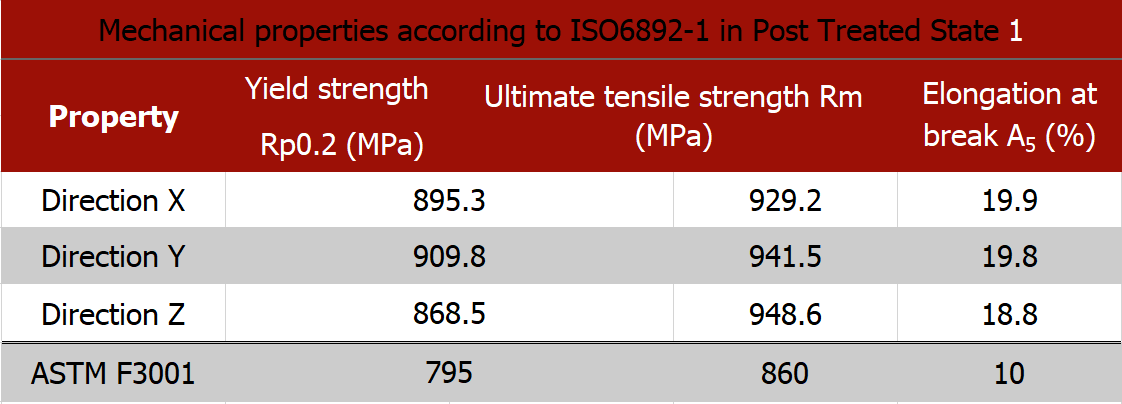
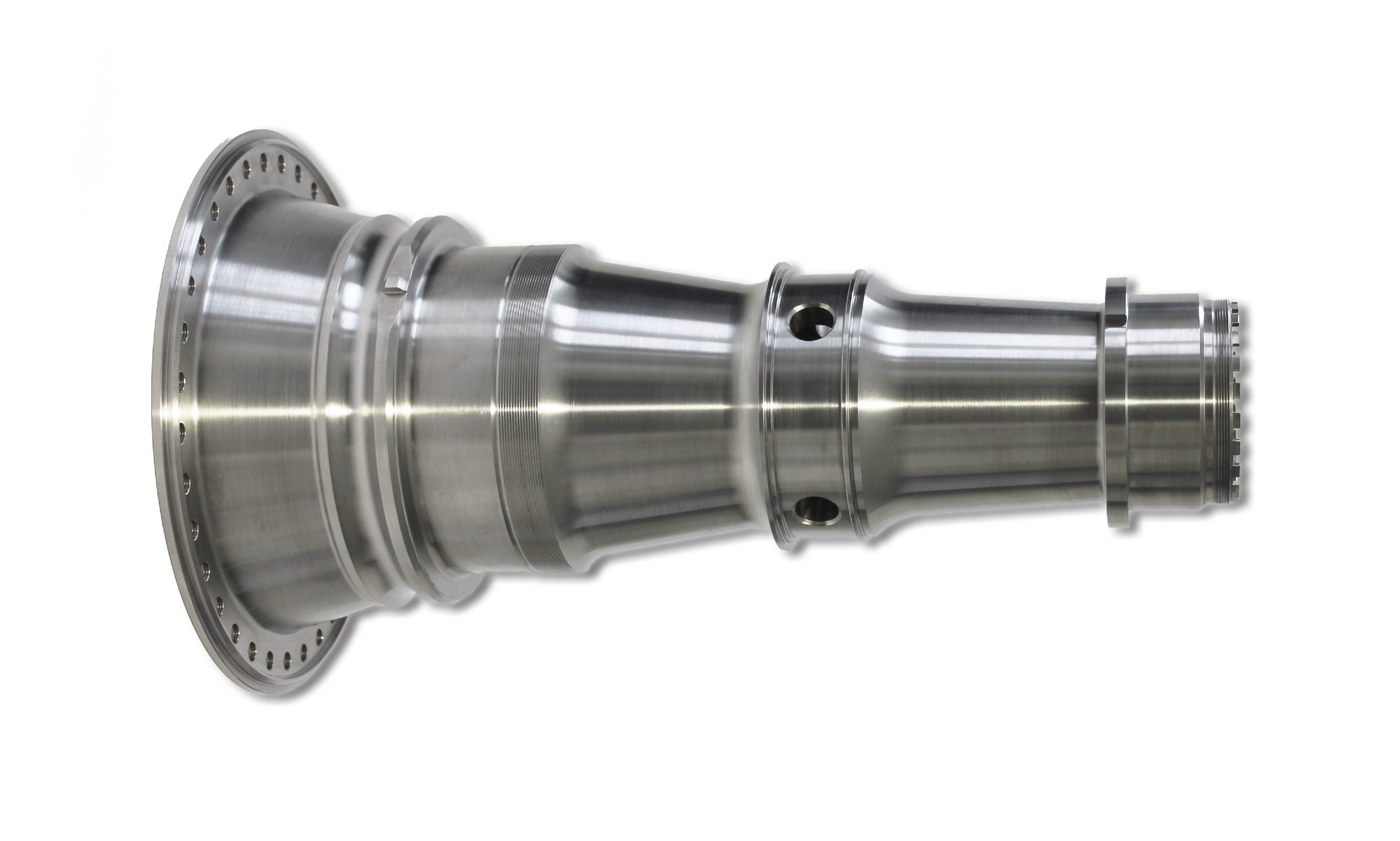