The innovative brake disc coating technology that fulfils
all technical requirements for the Euro 7 standard.
Even though the start of the Euro 7 standard with particulate emission limits for PM10 has not yet been finalized, Impact Innovations has already developed a solution with Impact Hybrid Brake Disc Coating® that not only complies with the 7 mg/km limit, but is also expected to comply with the 3 mg/km limit.
At the same time, Impact Hybrid BDC® withstands even the toughest cracking tests with combined corrosion tests without any delamination.
The Solution
With Impact Hybrid BDC®, Impact Innovations combines two technology worlds in one brake disc coating layer: The strong metallurgical bonding of a laser-cladded intermediate layer with the crack and corrosion-resistant cold spray coated top layer.
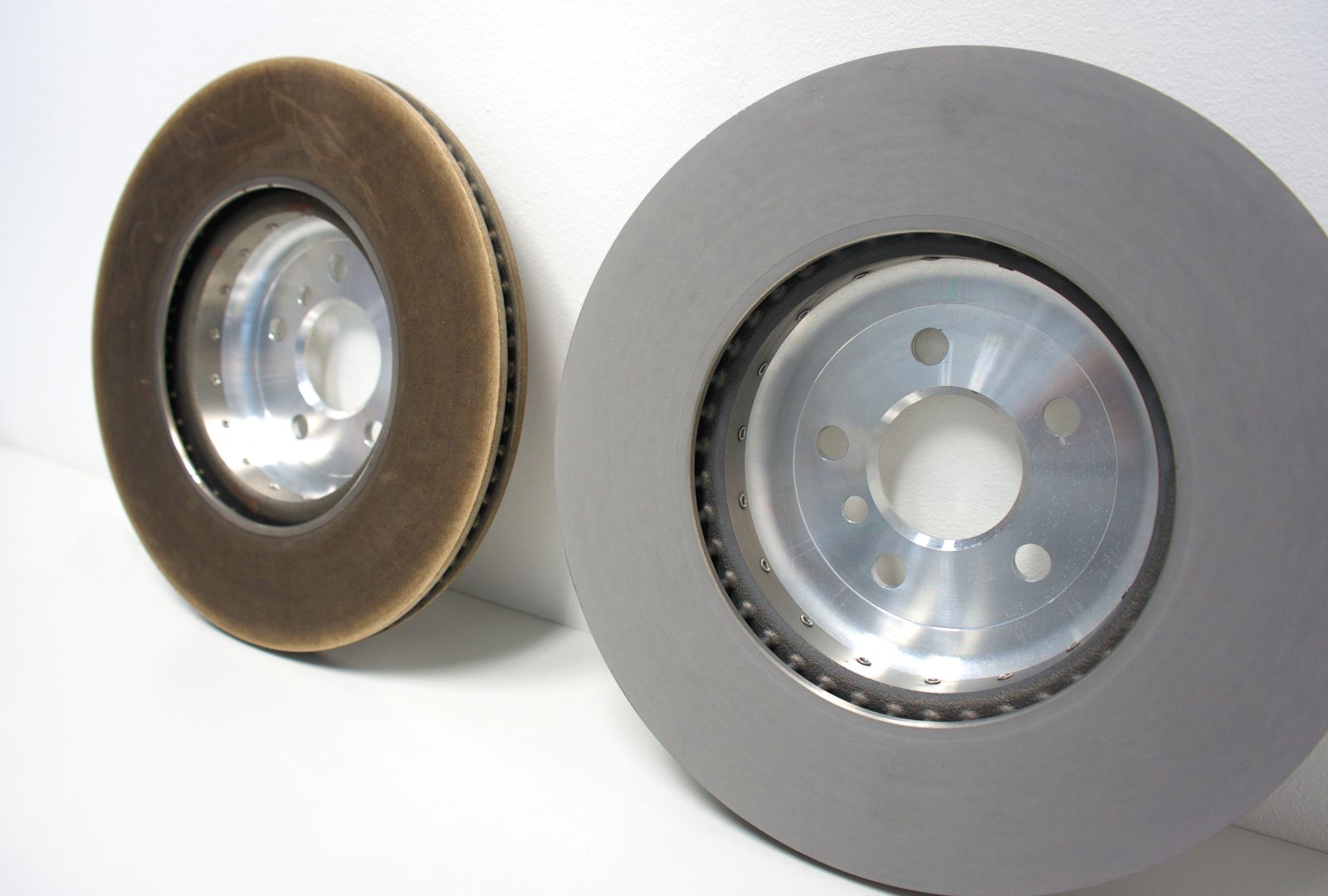
On the left, the brake disk with laser-welded intermediate layer. On the right with final cold gas top layer.
The laser-cladded intermediate layer requires no surface preparation to achieve the highest metallurgical adhesion strength to the grey cast iron of the brake disc. The thin intermediate layer has only limited thermal impact on the disc, so that thermal distortion of the disc can be avoided. At the same time, the surface of the intermediate layer delivers a perfect topology for applying the cold-spray top layer with similarly high adhesion strength without any further surface preparation.
The high kinetic energy when applying the cold-spray top layer reduces the tensions of the applied intermediate layer. In addition, with the compressed strength of the cold-spray top layer, a high-performance coating is built that leads to the highest crack resistance even under the harshest test conditions.
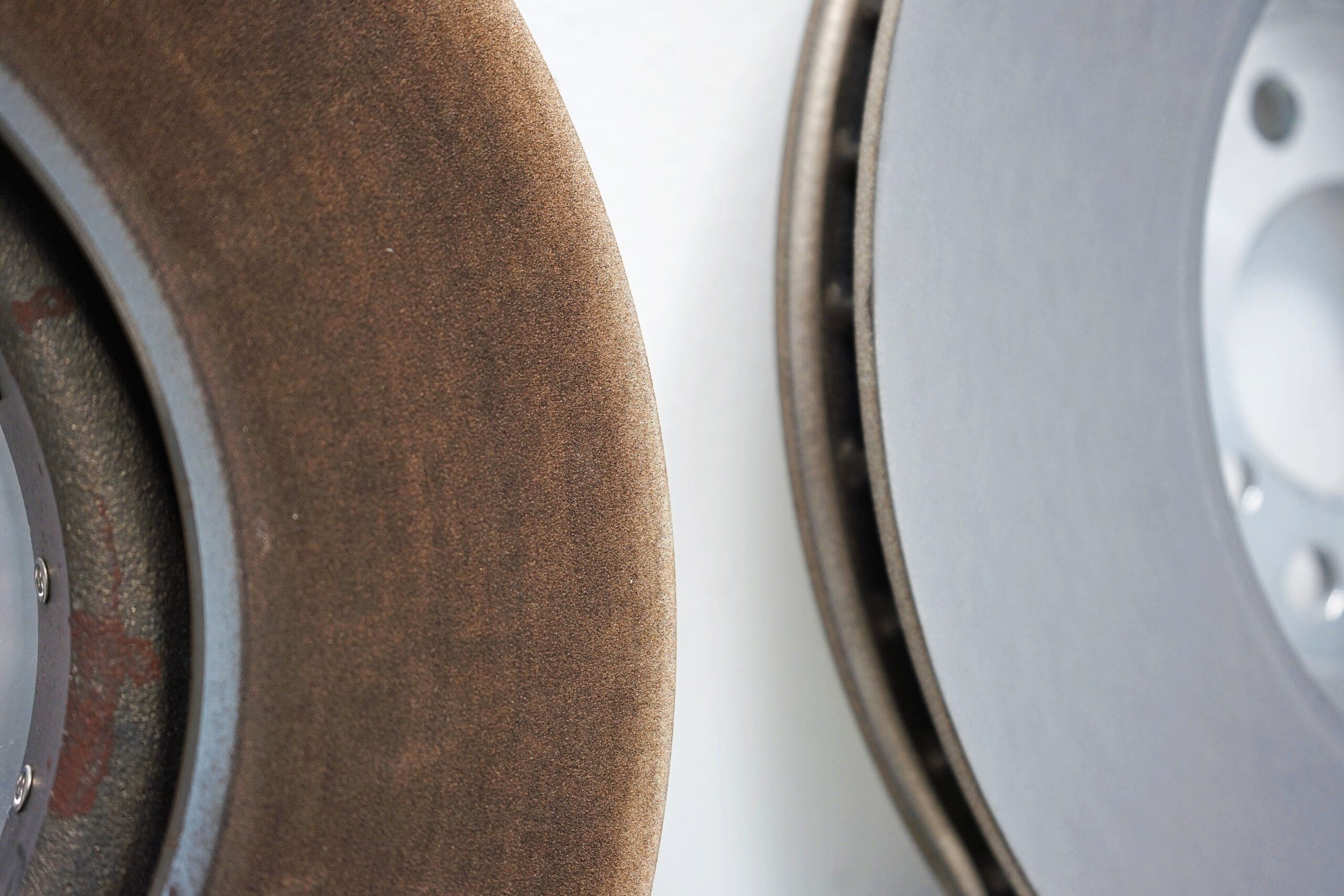
The Results
Impact Hybrid Brake Disc Coating® (registered for patent) prevents any severe cracking even at the highest brake forces and under corrosive environments. Therefore, corrosion at the interface to the gray cast iron disc and thus delamination can be ruled out.
Low-cost standard powders can be used for the intermediate layer. The titanium-based matrix material of the top layer guarantees the highest resistance against corrosion and cracks. Even up to 720 hours of salt spray test are passed without any corrosion.
The wide choice of suitable carbide materials in the top layer allows significant cost reductions by applying even low-cost carbides like silicon-carbide.
The surface temperature when the coating is applied and the associated thermal stress on the brake disc is reduced to a minimum so that no significant distortion of the disc can be measured (no umbrella effect, no deformation).
This leads to a reduced grinding allowance, which minimizes both the coating thickness (and the associated coating costs) as well as the grinding costs.
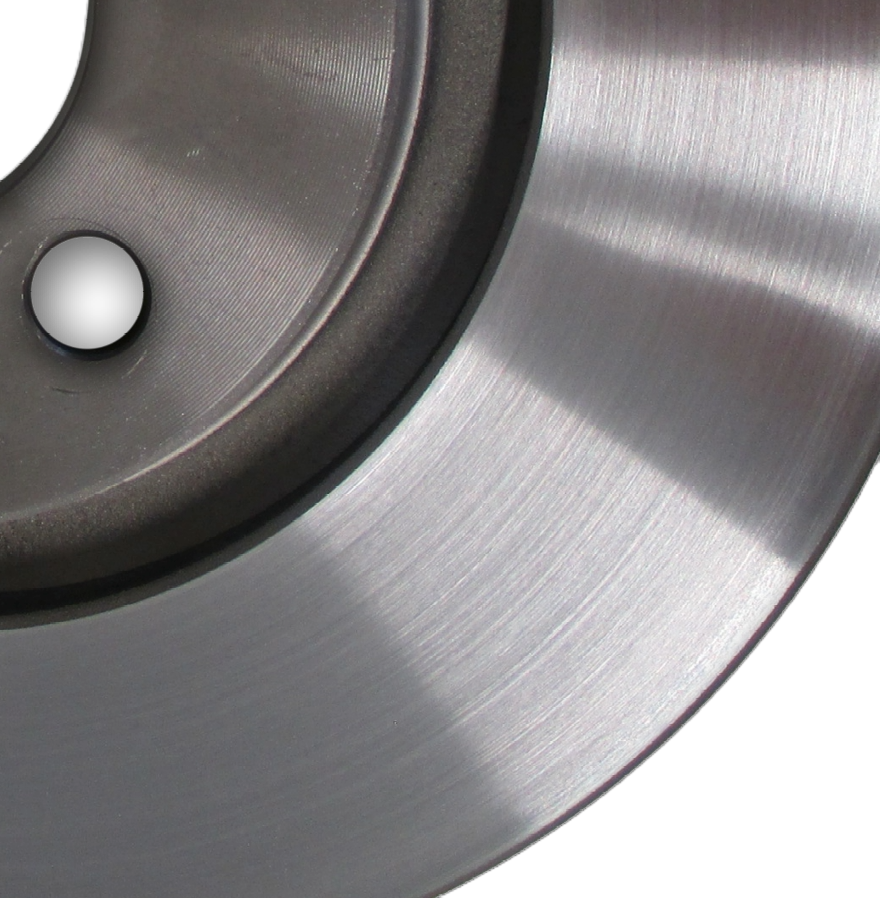
Together with the latest customized pad development from leading brake pad manufacturers, particle emissions can be drastically reduced, so that even the lowest emission limits below 3 mg/km can potentially be fulfilled. At the same time, these specially designed brake pads deliver very constant performance and desired friction values.
The Benefits
The Future
Meanwhile, Impact Hybrid Brake Disc Coating® is technically qualified by the BMW Group and other OEMs.
This means that Impact Hybrid BDC® is currently undergoing the final evaluation for series production by the BMW Group.
The Future
Meanwhile, Impact Hybrid Brake Disc Coating® is technically qualified by the BMW Group and other OEMs.
This means that Impact Hybrid BDC® is currently undergoing the final evaluation for series production by the BMW Group.
Press Contact
Dan H. Racek
Manager Marketing & Communications
[email protected]
+49 8636 695190-35